After the prior first ignition attempt for the EHT1 Micro End Hall Thruster, I made some simple modifications and went for a second full system ignition test yesterday to try to successfully operate the full thruster system again. While ignition was not yet verified, this test proved another step closer to full ignition, operating significantly more stably and with more intense plasma bridging than the prior test.
The thruster was first completely disassembled for cleaning and fueling. Fueling was the same as prior tests, with a small charge of Adamantane fuel poured into the heater cartridge. After fueling, the thruster was reassembled.
In order to run the hollow-cathode, the makeshift power board used in the prior hollow cathode ignition test was utilized and jumpered to the neutralizer auxiliary supply board. All other thruster preparations remained the same as prior testing.
The thruster was mounted into the vacuum chamber and pumped down. The rest of the test stand was set up for testing and livestreaming. There is a lot of work behind the scenes that goes into each of these tests!
Once vacuum was established heater power was first turned on and slowly increased to 5.5W of input power. After fuel flow was verified by the increase of pressure in the chamber, Hall thruster discharge power was turned on and brought up. Next, the neutralizer supplies were turned on and adjusted until a plasma glow was formed between the neutralizer and the thruster head. The supplies were continuously adjusted and main discharge power increased until the plasma glow was increased in brightness.
For this test, the plasma bridging was much more stable and brighter than the prior ignition test. In addition, no flashovers occurred on the boards or around the thruster. Despite this improvement, there was noticeable background plasma formation, and chamber pressure was higher than prior tests. Chamber breakdowns began to occur more and more frequently, although the thruster operated in this diffuse plasma background without much issue. The thruster was operated for a total of about 25 minutes before the test was ended due to excessively high chamber pressures and background plasma. While current was read on the Faraday cup, because of the background plasma, complete ignition could not be verified. The video below shows the successful plasma bridging during the test at peak plasma power. Note that this bridging is much more intense than the prior ignition test.
After the test, the thruster was removed from the chamber for inspection. Like the prior test, discoloration was present from the hydrocarbon plasma, however the deposit was significantly more noticeable compared to the prior test.
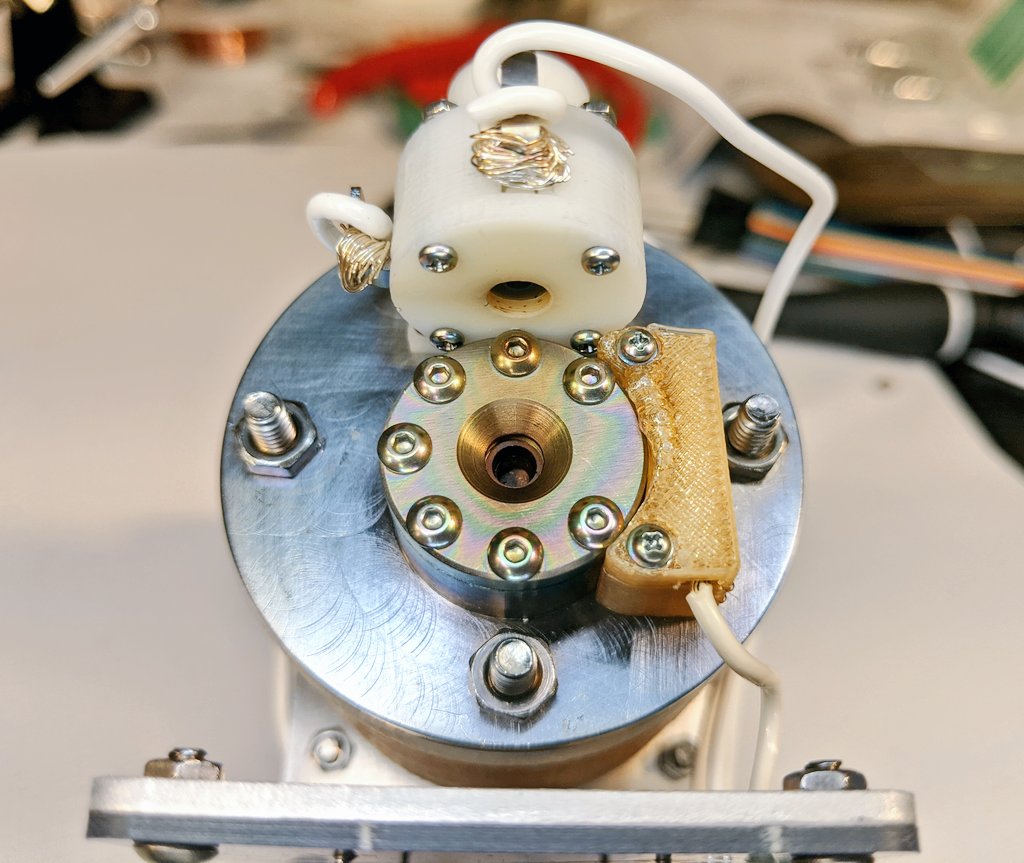
Removing the thruster head from the assembly, visible discoloration was also observed around the neutralizer fuel feed hole and fuel feed hole for the Hall thruster head closest to the neutralizer feed. This is indicative of plasma leakage back into the fuel feed.
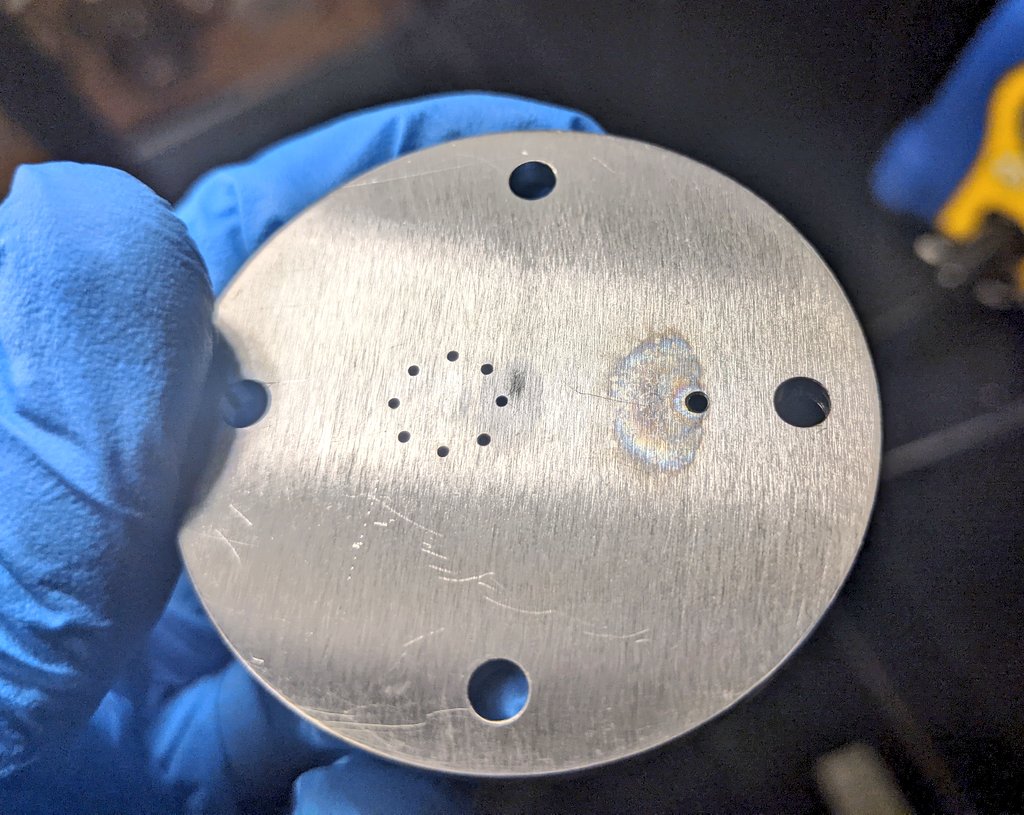
Disassembling the neutralizer, it was immediately observed that the anode aperture for the hollow cathode assembly was completely clogged due to carbon buildup. It is suspected that this was more severe than prior tests due to the longer run time of the cathode, as well as the higher overall background test pressures seen. A large amount of carbon deposit was further observed inside the hollow cathode itself. Removing the hollow cathode insert, noticeable buildup was present in the fuel feed channel, as well as discoloration due to plasma exposure from the increased backpressure due to the anode aperture clogging. However, despite the discoloration, no evidence of heat damage was present, and the carbon buildup and discoloration could easily be scraped off the surface.
Although I couldn’t qualify ignition fully due to the high background plasma from the increased pressure during operation, despite the better plasma bridging and beam being read on the Faraday cup, this test was another massive step closer to full system ignition. Moving forward, there are several additional modifications that can be immediately made to the system. Work is already underway prepping for the next test, and hopefully three times a charm!