Yesterday I ran the first ever full system ignition test of the AIS-EHT1 Micro End Hall Thruster! The thruster system included the high voltage electronics to run both the Hall head as well as the GDN1 neutralizer. While complete ignition and output beam was not yet achieved, this test marked the first major step in the development of this thruster.
Prior to the test, the thruster was completely disassembled for fueling with the Adamantane fuel charge. The thruster head itself was already wired up and ready to go, and overall assembly and disassembly of the system is relatively simple, with few components and mostly off-the-shelf hardware.
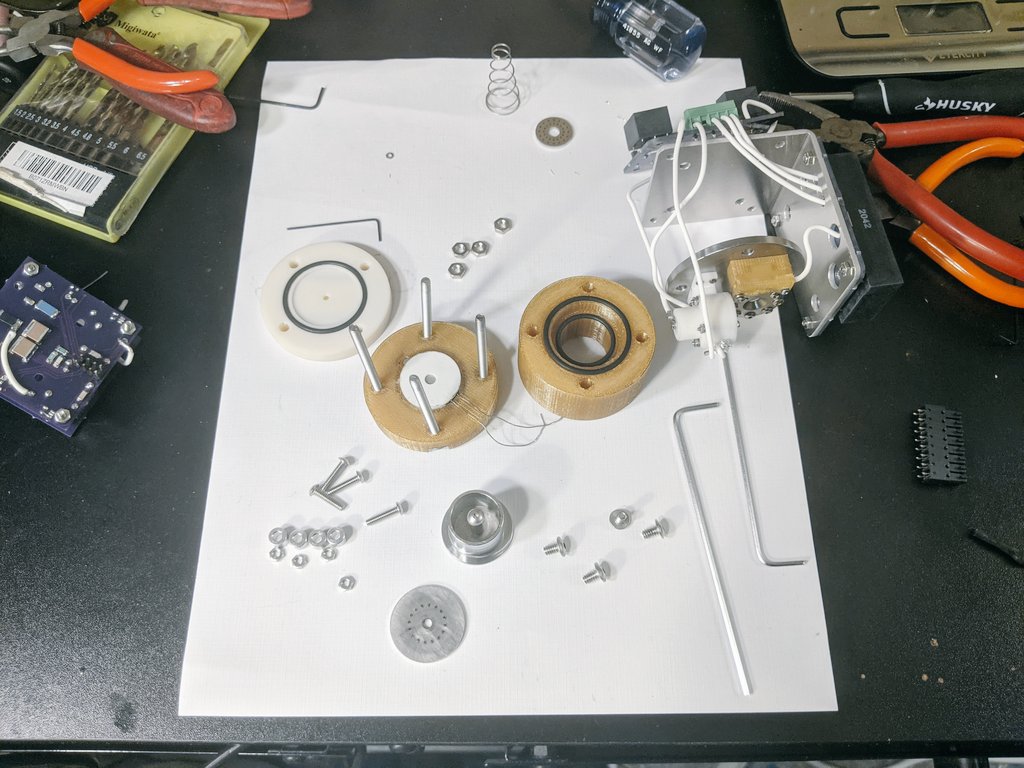
The first step is fueling the thruster with Adamantane. I could probably do this the night before since I don’t think that much Adamantane would sublimate away in air on its own, but since I don’t have a valve yet for the system best to do this right before testing for now. Here you can see the various steps of the process: pouring in the Adamantane granules, packing it down tightly with the presser plate, and repeating until it is nearly to the top of the fuel cartridge. For this first prototype tank, capacity of 3 grams of fuel is possible.
Next, the fuel tank is loaded into the housing, sealed up, and the valve housing (without an installed valve assembly for now) is put into place and ready to be bolted onto the thruster head.
During final checks and wiring I discovered that I actually mixed up wiring the anode and extractor electrodes on the neutralizer. That would have definitely caused the test to fail, glad I caught it in time! After that last-minute fix of what would have been a catastrophic test-failing wiring error, the system is ready to load into the chamber.
Here we see the thruster connected and ready for loading up into the chamber. I’ve got to say, going with a dedicated connector and wiring system for this test has made things so much easier! No more screwing around with a ton of sketchy wire connections, just one solid connector. After attaching the power and control connector and running initial bench checks, the thruster is positioned in the middle of the viewport, and the chamber is sealed up for pumping. Despite the fact that the complete EHT1 Hall thruster is incredibly small, with an effective volume of only 0.33U for everything, the thruster still just barely fits inside the 6″ conflat chamber.
Here we see a look at the full setup, ready for testing! For the time being, for this and subsequent tests the thruster will be controlled 100% manually with low-voltage benchtop supplies controlling the heater and HV supplies for the discharge and cathode. The setup is also prepped and ready for livestreaming, which I have recently started up again for my tests so that anyone can tune in and interact real time as I learn to operate this unique thruster!
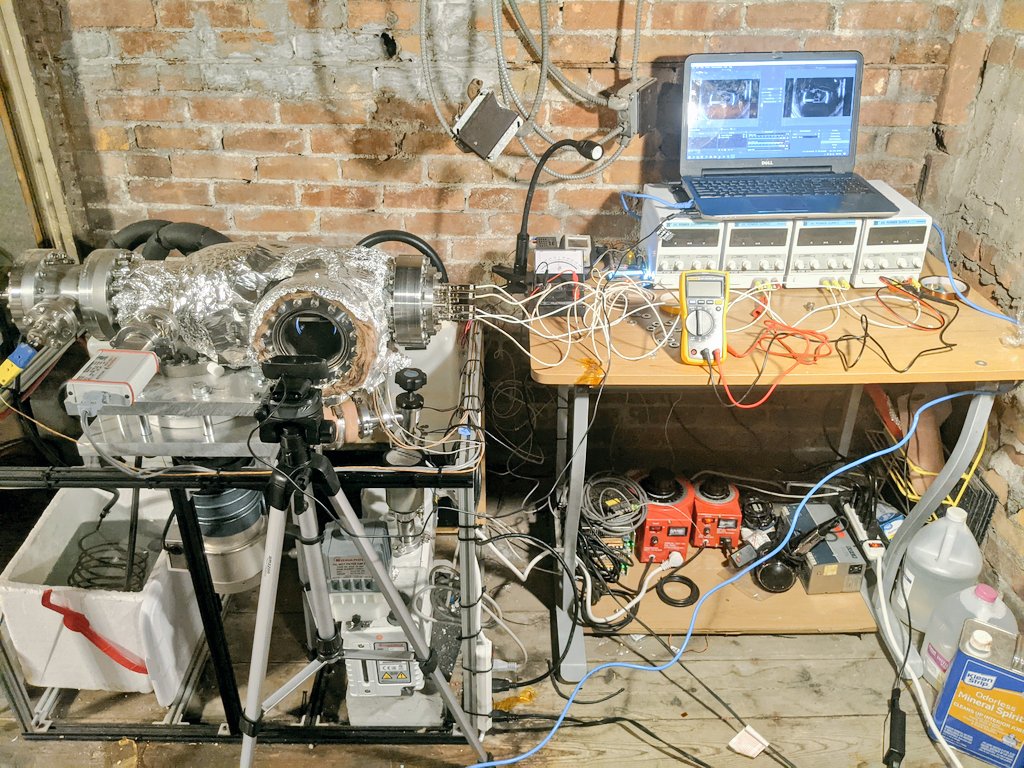
Since this was my first time operating the thruster, I did not know exactly what to expect. Although I had run numerous preliminary tests, as well as individual tests with a filament neutralizer and the hollow cathode by itself, putting everything together would still prove to have its own surprises.
Captured video from today’s full system ignition test of the EHT1 Micro End-Hall Thruster! Note this is not ignition yet, but we have plasma bridging, almost got there on the first go! Running the thruster and cathode together is definitely very different and a new challenge!
Heater power was first applied, and discharge power was brought up to a few hundred volts. After pressure rise was observed in the chamber, the cathode discharge supply was turned on, and discharge power further increased, until finally a light glow from both the thruster head and neutralizer was established. After this light glow was established, the extractor voltage was brought up, and all the supplies were adjusted to increase output from the neutralizer. A few minutes later, a large plasma flashover occurred along the outside of the thruster, resulting in catastrophic failure with a shower of sparks and termination of the thruster glow.
Upon further examination of test video after the test, it was discovered that the cascading failure event was initiated by a sudden e-beam burst from the neutralizer. While most of the beam was bent into the Hall thruster head at 90 degrees, a small fraction of the beam traveled past the head and continued straight, hitting the PEEK baseplate that held the Faraday cup. This triggered an immediate outgassing burst, which raised the local pressure enough for ionization to occur, causing a cascading plasma flashover.
Almost immediately after the initial ionization events due to localized outgassing from e-beam impingement, the plasma intensity increased significantly, followed by a yellow flash at the rear of the thruster, resulting in a shower of sparks. The entire sequence happened within a fraction of a second. After this explosive failure, the thruster supplies were immediately shut down.
After the failure, each of the supplies were carefully tested while still in the vacuum chamber to assess the damage. It was found that the main Hall thruster discharge and neutralizer discharge supplies were functional, however the neutralizer extractor supply was no longer functional. Despite this failure, it was decided to resume testing. Both main discharge and neutralizer discharge supplies were carefully turned up and adjusted. Eventually, the discharge grew brighter, and stable plasma bridging was established between the cathode and Hall thruster head. No beam current was measured on the Faraday cup, and despite the successful plasma bridging, a true exhaust plume was not observed, indicating failure to fully ignite the thruster. Despite this, plasma bridging between the cathode and thruster was achieved, marking the first step towards ignition.
The system was operated for several minutes, until the plasma suddenly cut out. After further power checks and inspections, it was determined that the cathode discharge supply had failed, ending the test. After the conclusion of the test, the thruster was removed from the chamber for inspection. Immediately, it was observed that the neutralizer extractor supply was the source of the explosive catastrophic failure during the first phase of the test.
Inspection of the Hall thruster head itself showed evidence of minor discoloration due to the hydrocarbon plasma output, but no major erosion or heating damage to any of the components otherwise.
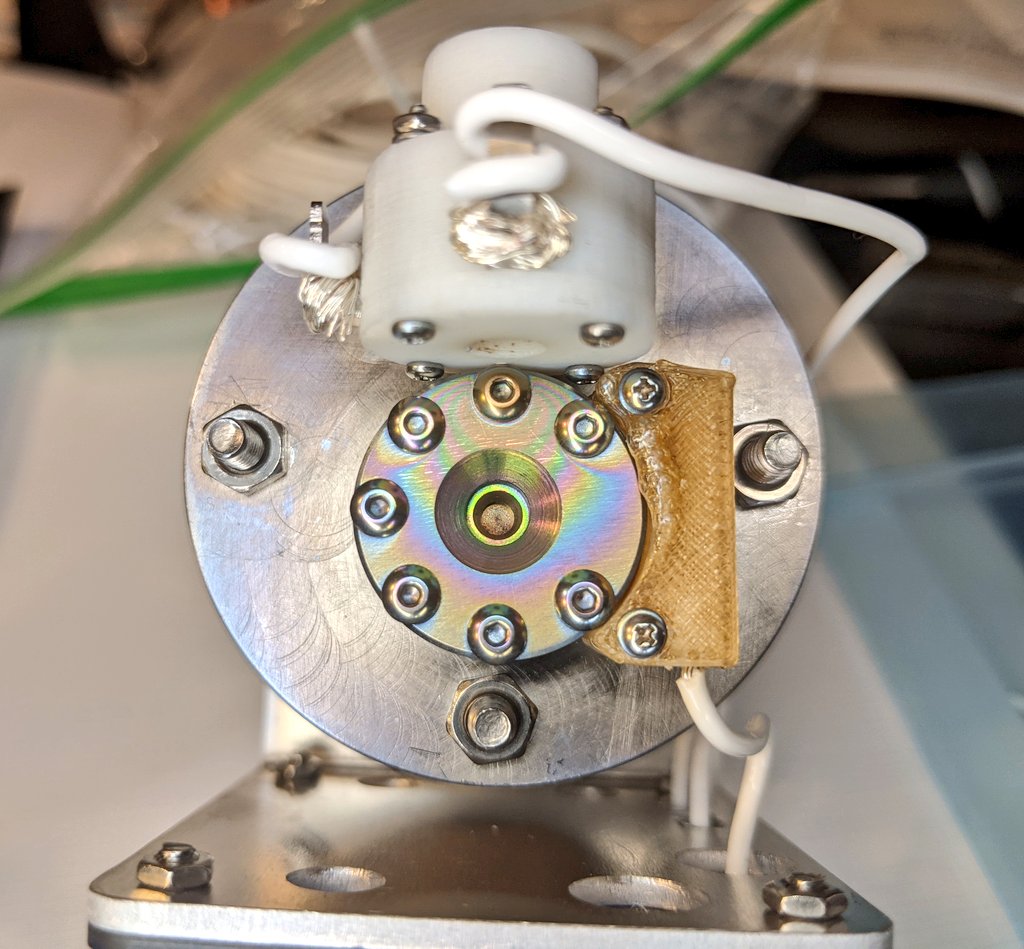
Full video of the entire livestream, as well as the captured explosive failure (full speed and slow motion), and several videos of the discharge are available on the AIS YouTube channel. Below is a link to one of the videos showing the stable plasma bridging during the test. While it wasn’t ideal results, it is still one step closer towards full system ignition!