On July 21st, I attempted the second ever fueling and ignition test of the AIS-ILIS1 ionic liquid electrospray thruster. Taking lessons learned from the first test, and using the new V5 board, I aimed at achieving more stable operation from the first try. This post will be an overview of the first part of the test, consisting of fueling and degassing of the porous glass emitter and reservoir, as well as qualifying my recently upgraded TVAC vacuum baking capabilities.
Fueling setup for this test was a bit different. For fueling, each of the porous glass emitter and reservoir are placed in their own separate beaker, just large enough to fit the 25mm diameter discs with tiny beakers. The beakers were then filled with ionic liquid just barely over each of the discs. The rest of each beaker was filled with 316 stainless steel wool to act as a baffle to prevent excessive splattering as well as keeping the discs from bouncing around. The tops were then covered tightly with aluminum foil.
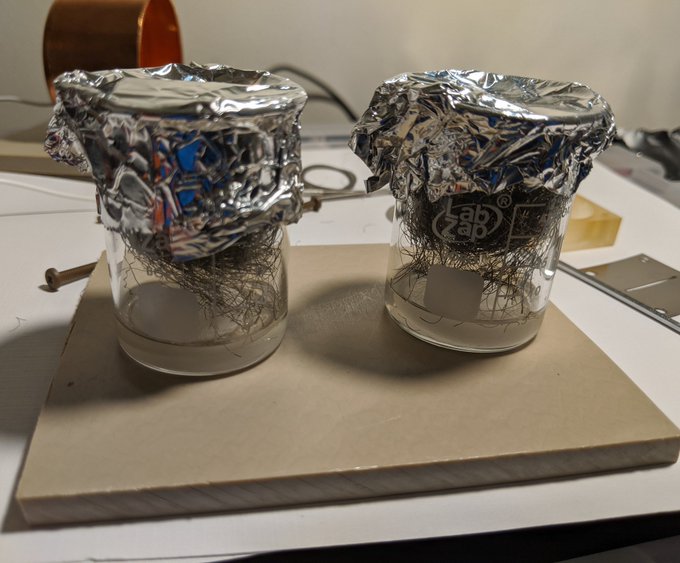
The filled beakers, as well as newly modified Ultem printed housing, and vacuum thermocouple, were mounted on a scrap PEEK baseplate that rested inside the chamber, to prevent direct heating from the chamber during bakeout. Baking was particularly important for this test preparation to better degas the plastic casing to prevent any spurious ionization due to outgassing as seen in the first ignition test, as well as better prepping the ionic liquid fuel. The system was pre-pumped with the roughing pump the night prior and sealed to facilitate faster pumpdown during the fueling phase of the test.
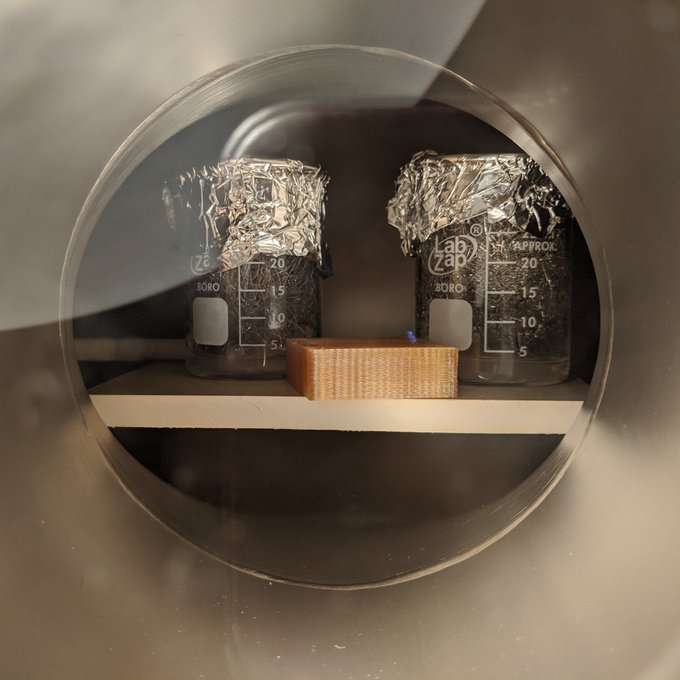
Finally, I decided to move away from computer monitoring with the MegunoLink program I have been using to standalone monitoring for the thermal and vacuum with dedicated hardware readouts. This will allow me to finally monitor vacuum and temperature while running the thruster at the same time, since before the monitoring software tied up communication and I could only do one at a time.
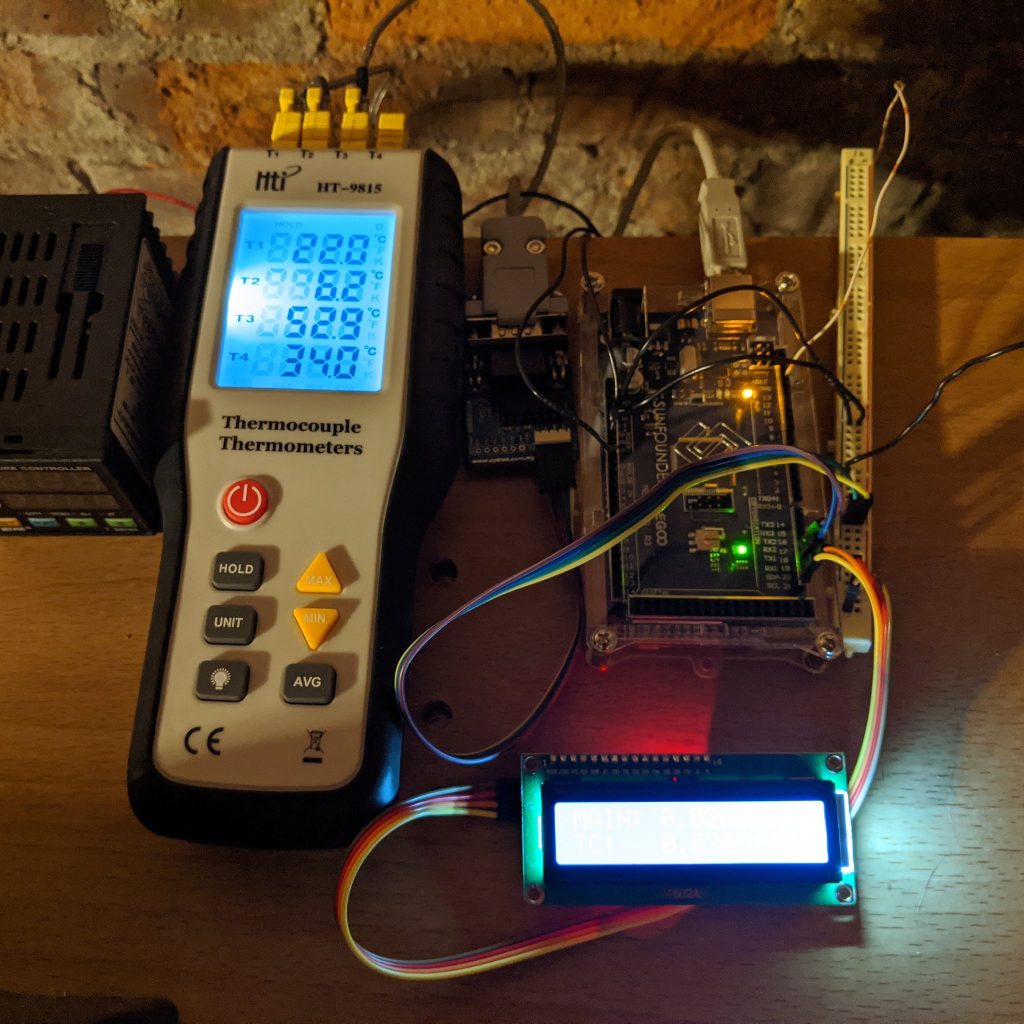
After grabbing a skid of ice for cooling the diffusion pump system during pumping, the pumpdown phase began. During the roughing cycle, the new heater system was warmed up. the heater was controlled with a simple variac and monitored manually, adjusting the temperature as needed. The large glass viewport in the chamber has a maximum rate of rise of about 2-3C per minute. Direct thermal conductivity to the viewport seems to be fairly low, and with just a single wrap of the heat tape on the viewport extension, heating could be brought up a bit faster while maintaining a slow rate of rise on the glass itself.
Pumping this time went much smoother. With significantly less fuel in each beaker, outgassing was greatly reduced. Though splashing did occur at the beginning inside the beaker, the stainless steel wool baffle proved excellently in mitigating spray, and the aluminum foil cover prevented any droplets from contaminating the chamber. The internal temperature was maintained between 65-80C for a duration of 3 hours, at which the chamber was kept at a vacuum level in the low 10^-5 Torr range. After the baking and degassing cycle was complete, and the system shut down and allowed to cool, preparations were made for the second phase of the test.

In the next post, I will go over phase 2 of the test, in which I attempted ignition of the ILIS1 for the second time.