Recently I completed the first ignition test attempt of the AIS-EPPT1 micro pulsed plasma thruster. this test revealed quite a bit of interesting challenges ahead with utilizing 3D printed housings for PPTs, with some surprising results, and some successful firing!
Let’s start off with video of the EPPT1 actually firing during the test! Note the much larger plume than prior PPTs, as well as the light-blue plume color:
And a captured shot of the awesome plasma plume from the system!
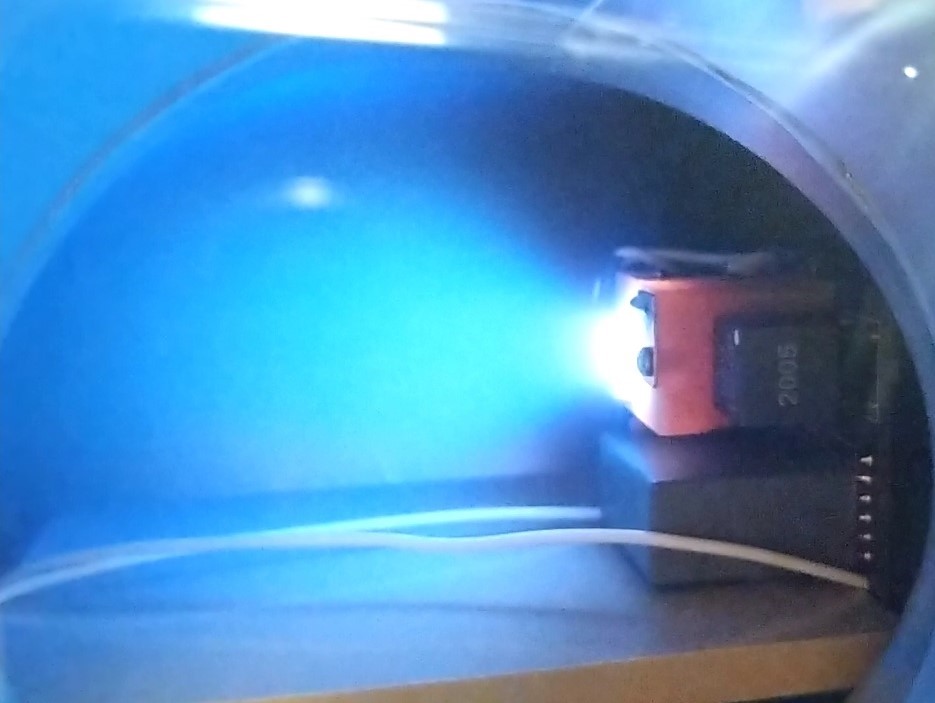
However, the thruster did not start up firing immediately. In fact, I experienced a large series of unusual breakdowns prior to firing, which only occurred briefly before failure of the system.
Here we can see video captured before successful ignition, where there is arcing from the igniter pin to the anode (which is quite unusual), as well as arcing from the igniter connection to the board. In both cases this tracks in the outside of the 3D printed housing.
In the second fault observed prior to ignition, we see a very interesting phenomenon, with multiple arc points flashing up along the side, starting at the igniter connection tip and traveling down along the surface to the board. This also stopped after some time. Here we see the external arc fault captured from the second video. This arcing failure actually subsided after several initial pulses, indicating this may have been caused by outgassing. Notice how the arc travels around even the 90 degree bend between the igniter and anode
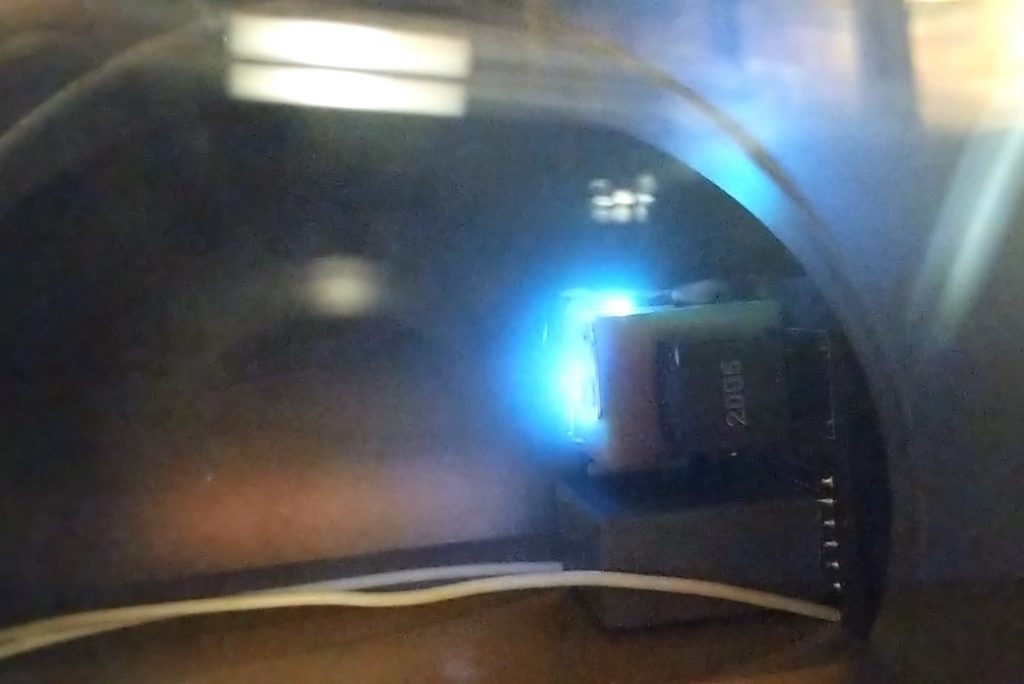
Another external ionization pulse occurring around the igniter connection, looking like it is actually blowing upwards through the Ultem housing. This may be attributed to arcing through the case between the igniter and internal anode wire
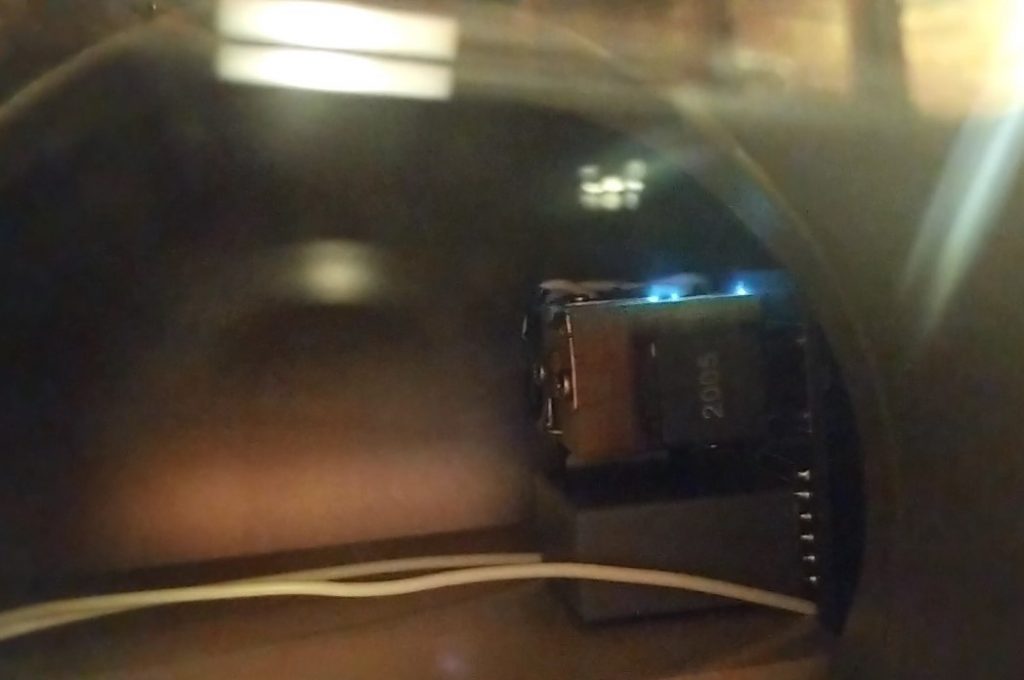
After successful ignition firing of the thruster for a short period, I observed the igniter arc flashing, but no ignition. In this video, we can see the igniter starting at high rep rate, as I decrease it to lower rep rate. Flashing is occurring inside the Ultem housing, between the layers right under the anode rail.
Here we can see a shot of the internal arcing:
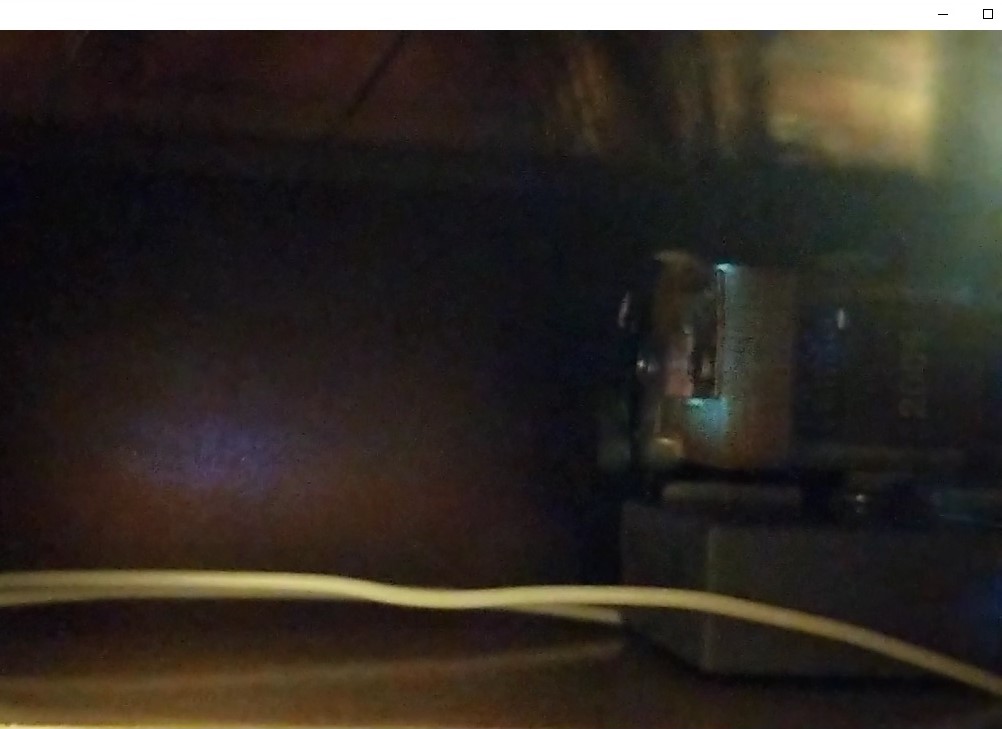
This test has provided a ton of data moving forward. It first confirmed that successful ignition can occur and that the basic design works. Despite my initial hesitation about the electrode spacing, this appears to not be a problem, allowing me to keep the larger fuel block. It also shows that the igniter pulse was quite a bit more intense than expected, which confirms the igniter circuit improvements over the gPPT3. The arc was more than enough to ablate the Teflon, and was actually high enough voltage/energy to cause some interesting faults.
This test does show however the challenges of 3D printing the housing for this type of thruster. While no issues occurred with the ILIS1 at +/-5kV, with this 10kV ignition pulse, it appears the arc is making its way through the print, despite being “solid” infill. Interestingly, despite the numerous arc faults that occurred during the test, there is no evidence that any components have actually broken on board yet. In particular, this new thyristor took a beating, and while requiring more oomph to fire, has proven very robust.
While only a few tens of shots were achieved, so far the primary and ignition pulse capacitors have also proven to handle the initial pulsing. The first goal will be passing the 1.2k shot record from the gPPT3, after which I will work towards achieving 10k initial shots. Finally, the test confirmed that the pulse igniter for this new design for the smaller “A” version can sustain high rep rates at up to the max rep rate spec of 3 Hz, a huge improvement over the 0.3Hz rate if the older gPPT3.
Once I fix the external arcing issues and get it running stably, I can proceed to both thrust measurements with the micro pendulum as well as lifetime. Despite being the same energy as the gPPT3 at 0.1J, the plume is significantly larger. Overall, I am very happy with this first round of testing, and am much more confident that the new ePPT1 design will exceed the performance of the old gPPT3 while being lower cost and more accessible.