In my prior blog posts, I shared updates regarding the new and much anticipated V4 design of the AIS-gPPT3-1C Pulsed Plasma Thruster module for PocketQubes. With the thruster assembled, checked, and mounted into the chamber, testing was ready to go without issue, and was attempted yesterday. Unfortunately, not every test is a success, and this particular test ended up being a lost battle.
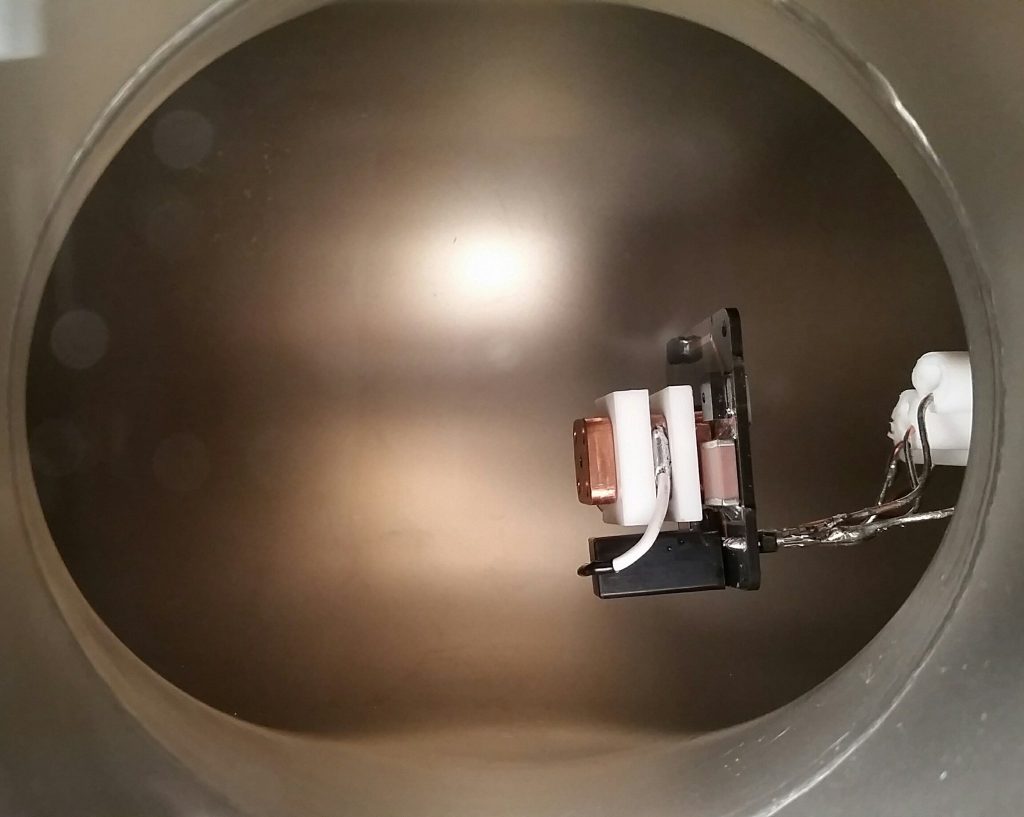
As a bit of background to the test, this was to be a big and key test to push the lifetime limits of the electronics I have encountered previously. At 3Hz, the main bank should be around 650V, much less than its rated 1kv (2kv peak). The last test lasted only 1300 shots straight, so with the greatly derrated voltage of the main bank, I was looking to hit my first major milestone goal of 10k shots. In addition, the ignition voltage had been pushed much higher, driving the ignition part to twice the voltage from prior tests. From the last test, I had to power the circuit at 4V in for reliable ignition. This time, I am set the circuit for nominal operation at 3.3V max for at least 85% ignition reliability. Assuming a generous 25% misfire rate worst case scenario, at 3Hz I would surpass the 1300 shot mark in about 9.5 minutes, or less than 7.5 minutes at 0% misfire. If it managed to survive without any electronics failures, I could reasonably expect to finally pass the first true lifetime milestone of 10k shots in less than 3 hours. This would bring me to about 10% of the rough estimated fuel shot lifetime.
The first major troubles started with pumpdown. The day prior, I had pre-pumped the chamber to nominal roughing levels without any issues. Yesterday, during the actual pumpdown, roughing was way too slow, and highly abnormal. After almost 2 hours of pumping, and troubleshooting the system along the way, it was determined that the roughing pump seemed to have a failing seal, causing significantly lower performance. As a result, the diffusion pump was pushed to dangerous foreline levels to achieve high vacuum. By dangerous levels, I mean I was really pushing the system to safe operating levels of the oil. The oil I am currently using is 705 diffusion pump oil. Very robust oil, but for the EO4 pump the max foreline pressure is 500 milliTorr. For reference, despite this being the max pressure, you should ideally never operate the pump at that high foreline. Well, to get results, I decided to push it right to the wall. At the highest point, pressure peaked past 500 milliTorr for a brief period. Really, really bad. Although after the outgassing phase of the oil, the pressure shot down to 10^-5 Torr in a matter of minutes, it was still a very risky move. I will need to open up the pump at some point and inspect the oil to see if I cause any oxidation or damage as a result.
Once at 10^-5 Torr, it was time to start the test. Start up procedures were initiated, power was applied, and… nothing. Absolutely nothing. I tried pulsing the thruster again and again. A couple of spurious blips of plasma emanated from the thruster, but no ignition. Finally, to add icing to the cake (or salt in the wound I guess in this case), the bank readouts went to 0 volts, indicating a failure on board, most likely a short.
This was an unfortunate setback, and a huge blow to the AIS-gPPT series effort. While the V4 design was expected to significantly improve performance, and overcome failures of prior versions, it turned out that this update ended up being the worst yet. Not all tests are a success, and I had a great streak prior. Going forward, I will need to consider where to take development from here. Despite this, I am eager to continue pushing forward with these efforts, and break boundaries in the field of propulsion.