So it’s come to this. In order to advance the ILIS1 development to the next stage I’ve had to take matters literally into my own hands. Got some diamond burr Dremel bits and free-handed the ridge into a 0.6mm wide tip, 2mm square base pyramidal spike. Not bad for my first go!
This ended up being way easier than I thought. The bits machined through the porous glass like a leaf blower through a sand castle. I have had a lot of trouble getting custom machining for this new geometry, and am honestly wondering why this is so exorbitantly expensive or difficult to do.
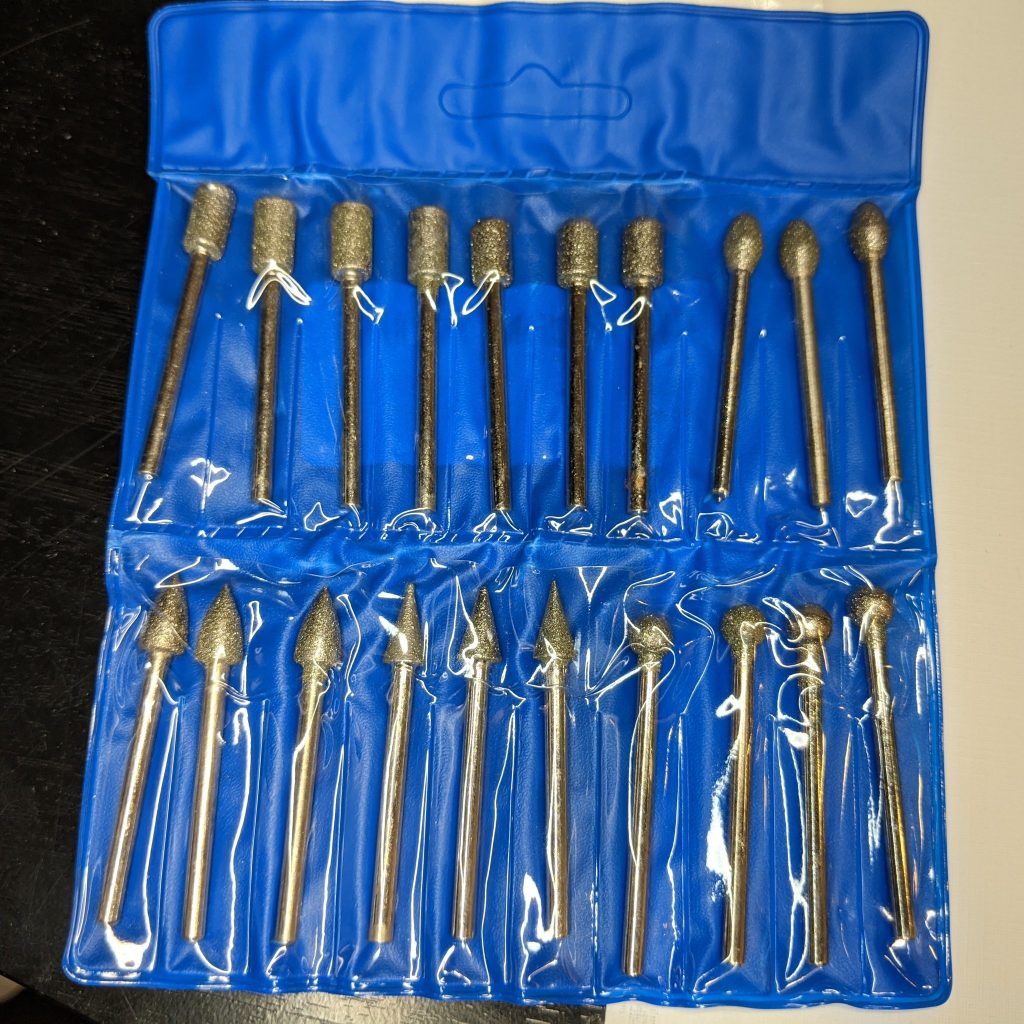
I could have gotten the tip even finer, but it came out good for my first try and I didn’t want to push my luck. I am seriously considering buying a cheap desktop micro mill or CNC and doing the emitter manufacturing in-house. Save a ton of money, and no 3-4 month lead time.
Ideally I want a 1mm square base (2mm may be acceptable) with 0.1mm tip (ridge was originally 0.1mm wide at 20mm long, and I shaved the length to 0.6mm), 1.5-2mm high, but I’ll take what I can get for now. If this works well, it means it works for a worst case machining scenario.
So why spikes? Significantly higher field strengths, higher packing density, and emission just naturally wants to occur at the tip. I should have really started with spikes, but I went into this project learning from nothing, and started with the hardest geometry to get running. If we look at data in literature, the trends are moving to and settling around spike arrays for macro-ILIS (like it’s already well established micro-ILIS counterparts). Typically 3uN per spike can be expected, however they can apparently achieve up to 7-9uN of thrust per spike.
I am already gearing up for the next big ILIS test soon. The new shield electrode, as well as various sizes circular aperture extractors (1mm, 1.2mm, and 1.4mm) have already been ordered and will arrive next Friday. The goal of this next test will be to match 3uN of thrust or exceed it, and establish longer operating times at this thrust level. This test will also be the basis for my new tentatively named AIS-ILISX thruster design, which the conceptual design will be revealed tomorrow.
It’s a massive challenge doing this level of thruster development at home with almost no funding, but it’s forcing me to get extremely creative and resourceful, and get to really know every aspect of the system as I brute force my way to a competitive thruster one step at a time.