On July 21st, I ran the 2nd ignition test for the ILIS1 ionic liquid electrospray thruster. My previous post detailed the actual test phase itself. While I did not achieve complete emission, it is a huge improvement with actual controlled partial emission from the thruster on the +HV cycle. Here is the full video of the test. More details below!
Here we can see captured video of the ILIS1 in action. Due to the -HV side failing early on, only emission was seen during the +HV cycle (hence the several second pause between firing.) Power was started out low, and gradually increased. One interesting thing to see is the thruster failure at the end of the video. I slowly raised thruster power, but it eventually suffered a catastrophic short. This is actually a quite rare opportunity to view first hand a key failure mode of an electrospray thruster in action!
Here is a captured shot of the ion beam plume. Emission occurs from the far corner, with each voltage cycle at 5 seconds long. A very clear and bright plume from the ion beam emission is present. Ideally, when full and complete ignition is achieved, the entire extractor slit would light up with a large plume emanating from it.
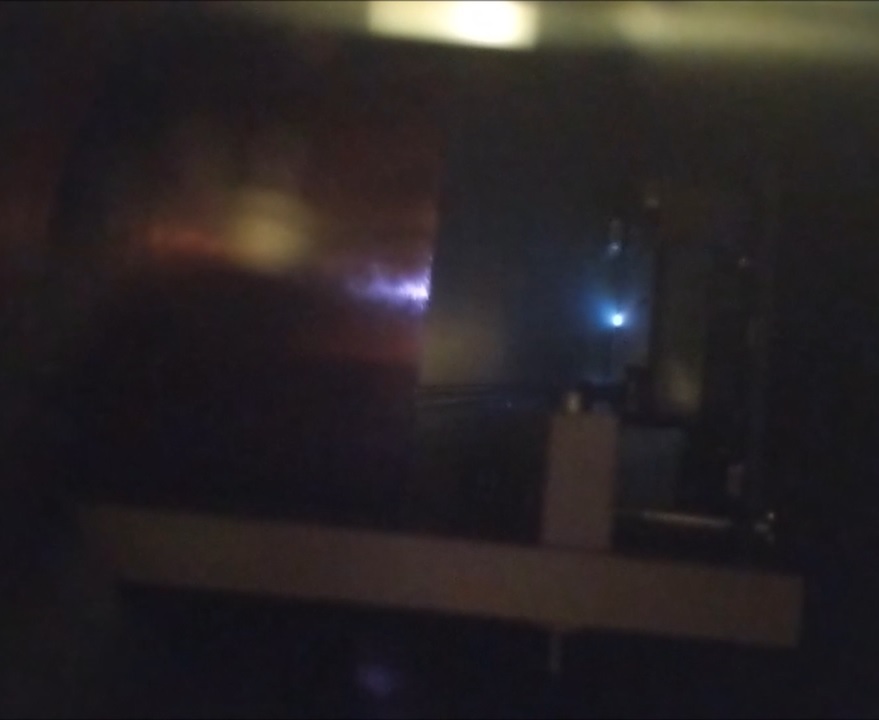
During some earlier warm ups, I did actually still see some minor flashes coming from the back of the board, which could indicate some clues for the -HV side failure. Here we see some emission, then a few flashes and it starts to cut out before I readjust the input.
From these short videos, it is very clear what needs to be done moving forward. It is apparent that field strength at the ridge emitter edge is too high. This is due to a combination of geometry as well as potentially poor cut quality of the laser cut extractor (some tiny burrs in the cuts).Work is already underway for modifying the extractor geometry to significantly reduce field strength at the edge, and focus it more along the central portion of the ridge. I am also looking into new suppliers for much higher quality cuts, potentially going with stainless PCB stencils instead.
This is also the second time the -HV supply has given me issues, and it was acting a bit weird during preliminary testing, so I will need to probably order a new one, since this supply has undergone a tremendous amount of abuse during testing.
On the PCB side, I will be adding surge protection resistors to limit any arcing current due to stored energy in the main HV filter caps, as well as widening the Pico rise/fall time with larger input capacitors to further smooth out the transition for stability.
My predictions from last time were also very good. No outgassing issues were observed from the new degassed Ultem 1010 printed casing. Turn on voltage was about 2.2kV, which is exactly where I was expecting. Adjusting the spacing, and using a thinner aperture also allowed for partial ignition to be achieved. In addition, slowing down the transitions as well as increasing on time per cycle massively increased system stability, having only one glitch during the test at the beginning (most likely when the -HV supply failed.) Running the thruster was much smoother and easier this time around.
The key things to address are evening out field distribution on the edge, and further limiting instantaneous energy of the system in operation. New extractor designs and boards are already underway. Solving these issues, I should have stable emission and complete ignition across the emitter hopefully within the next test iteration or two.
ILIS electrospray thruster technology is a massive challenge. However, this is only my second attempt ever literally from scratch, and I am halfway to stable emission. This will be a very iterative process, but with each test I move closer and closer on this thruster! Places like MIT, Accion Systems, Ienai Space, Amazon, as well as many other well funded and prestigious academic labs around the world have invested many tens of millions of dollars and decades of work combined into ILIS thrusters. I am now at the cusp of my own ILIS thruster on pennies at home. The AIS-ILIS1 is coming, ion by ion.