After modifications of the ILIS1 ridge emitter to a single spike emitter for the ILIS-X1, I attempted several tests to qualify emission from the spike. Unfortunately, I have been plagued with numerous failures, and as of now, have yet to achieve beam from the system.
The first attempt occurred on October 29th. The thruster utilized a 1.2mm diameter circular aperture, with the prior tested shield electrode for the emitter disc.
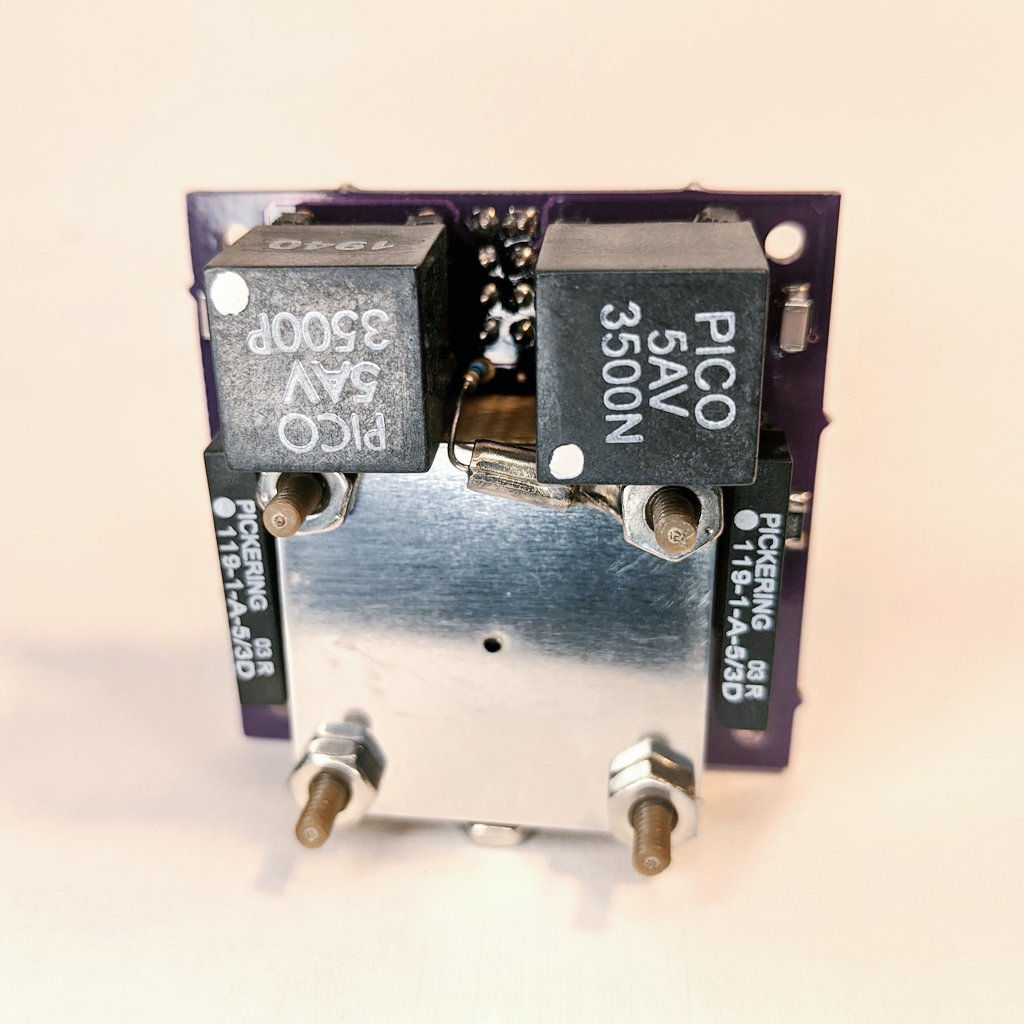
Upon starting up the thruster, I immediately got an unusual ionization glow inside the 3D printed housing with the tank and emitter. When I tried cycling the voltage, the negative side failed to function properly. I disconnected all of the inputs which should completely disable the thruster, but was still getting very unusual readouts from the thruster. I then disconnected the power for the HV relay and power supply enable control, and turned up HV supply voltage, and started getting some HV output. I suspected that the control mosfets were shorted, and that ionization glow was due to both supplies being on at the same time. While I did eventually confirm some minor beam briefly, the system eventually went haywire and I had to shut it down.
After this test, I decided to completely rebuild the board from scratch. For this build, I decided to switch to the largest 1.4mm diameter aperture, and adjusted the emitter-extractor spacing from 0.1mm to 0mm. With the wider aperture, it was much easier to align the spike emitter right in the center.
The second test with the spike emitter was conducted on November 7th. Immediately powering on the board however, I experience almost instant failure, with the thruster readouts indicating shorting in the system.
After this test, probed around on the board, discovering an issue with the load switch used to power and enable the thruster HV supply. As a result, I modified the board to completely bypass the load switch, directly powering the HV supply with the input voltage.
The thruster was loaded back into the chamber, and a third attempt was tried on November 12th. Again, turning on power, I experienced almost immediate catastrophic failure. This time, there was shorting at one of the corners. Taking apart the thruster later revealed that it had arced through the thin 3D printed Ultem housing, tracking right along the surface and shorting between the emitter and the extractor.
Three major failures in a row back to back with the ILIS-X1 prototype. It was a bad month for testing, however it forced me to consider changes moving forward. Primarily, I decided to move away from 3D printed housings for the ILIS development to solid CNC machined PEEK hardware. This is the direction I wanted to go originally, but cost significantly more. Unfortunately, I have had so many issues with 3D printing across numerous builds that it is time to retire it for parts that interact with HV directly on the thrusters. Second, I will need to redesign and further simplify the board, moving away from any switching and focusing on pushing forward in monopolar mode with a neutralizer.