Yesterday morning I ran the first ever ignition test of the EHT1 Micro End-Hall Thruster LIVE to great success. During the test I established stable discharge and beam at only 2W discharge power using actively sublimated Adamantane and a Tungsten filament neutralizer! The full livestream with live chat commentary is available on the AIS YouTube page, and can be viewed below. I will also recap some of the test highlights, as well as pre-test setup.
The EHT1 can be seen here being prepped for fueling and assembly as well as running final HV and power supply bench checks for the big ignition test tomorrow morning. All the parts are cleaned and ready for assembly!
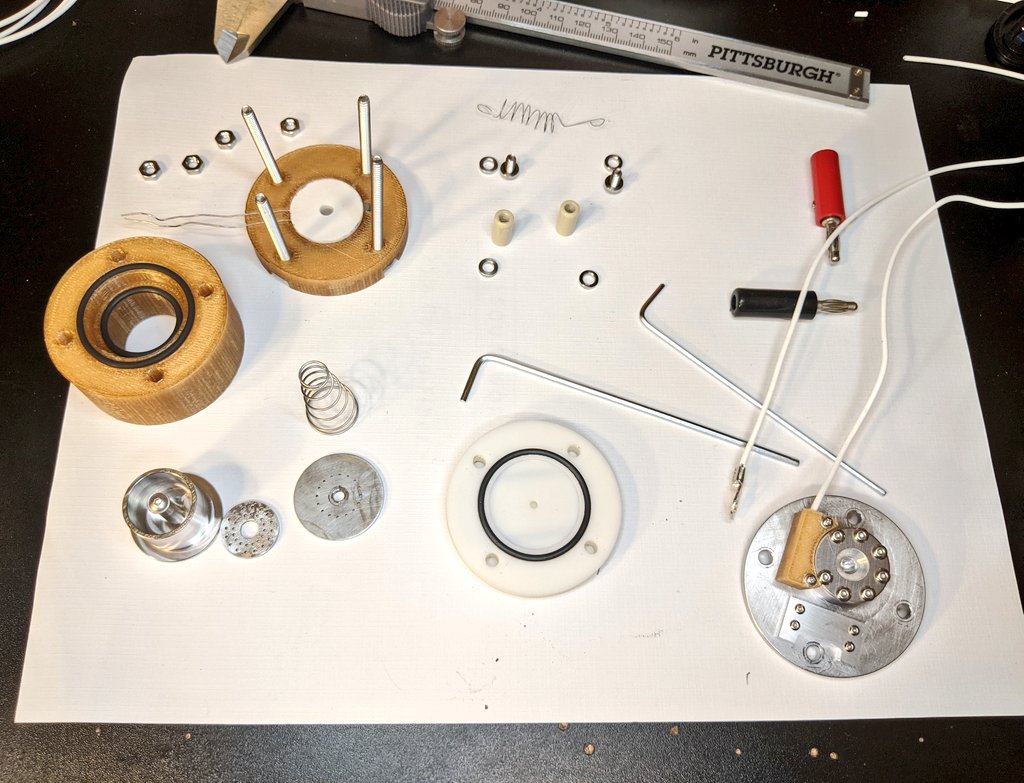
First things first – fueling the thruster. 2 grams of solid Adamantane were loaded into the heater cartridge, and the Sublimation Fuel Delivery System sealed up.
After fueling, the full thruster was bolted together, simultaneously compressing all the seals. I had the valve housing as well to test flow rates at full open, however I did not have any valving installed, so this would be similar to my preliminary ionization tests I ran earlier.
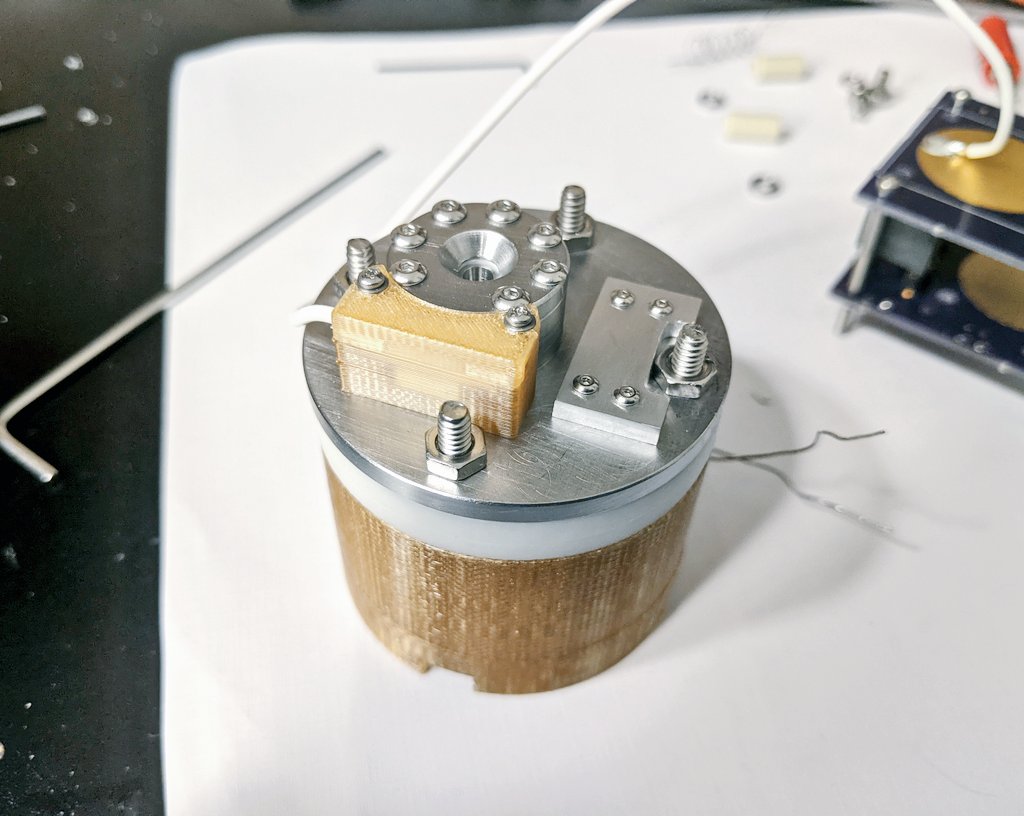
Next, the Tungsten filament neutralizer was wired up. The thruster was now ready for mounting in the chamber and final electrical connection testing before pumpdown.
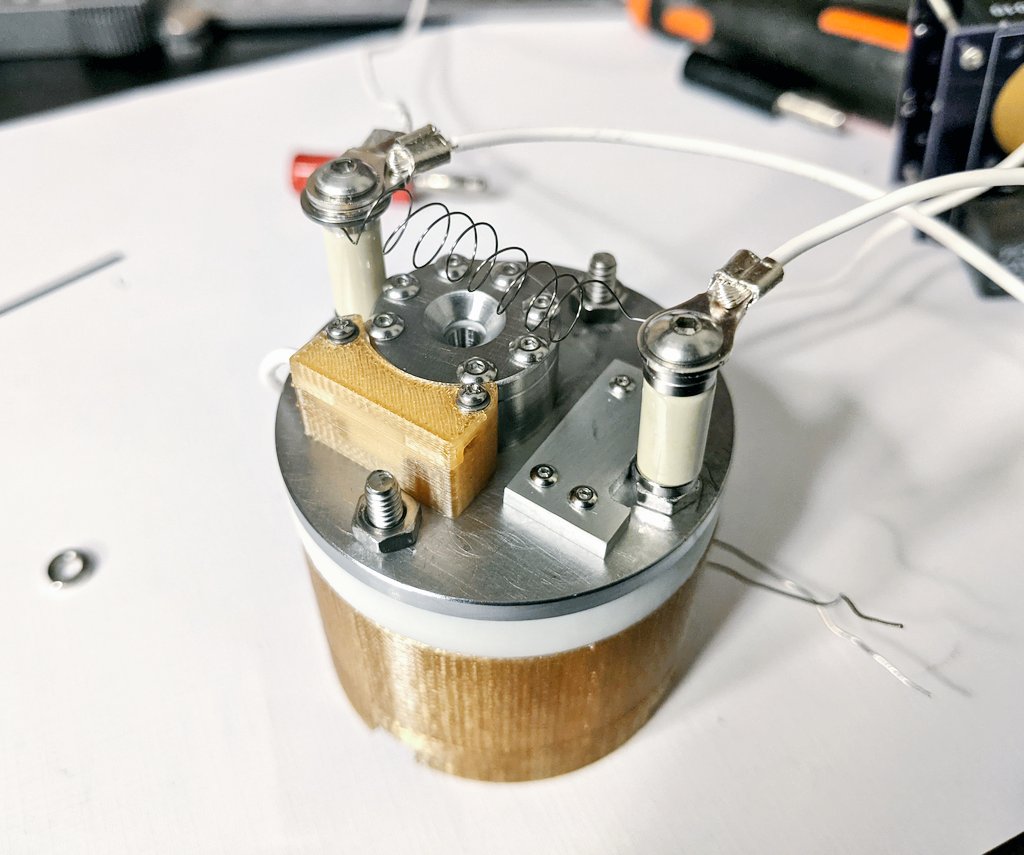
The thruster was mounted and wired up into the chamber, connections checked, and pumpdown began! Unfortunately setup took longer than expected being my first time ever configuring my system for running this thruster, and my current 6″ conflat based chamber is almost too small for this thruster setup.
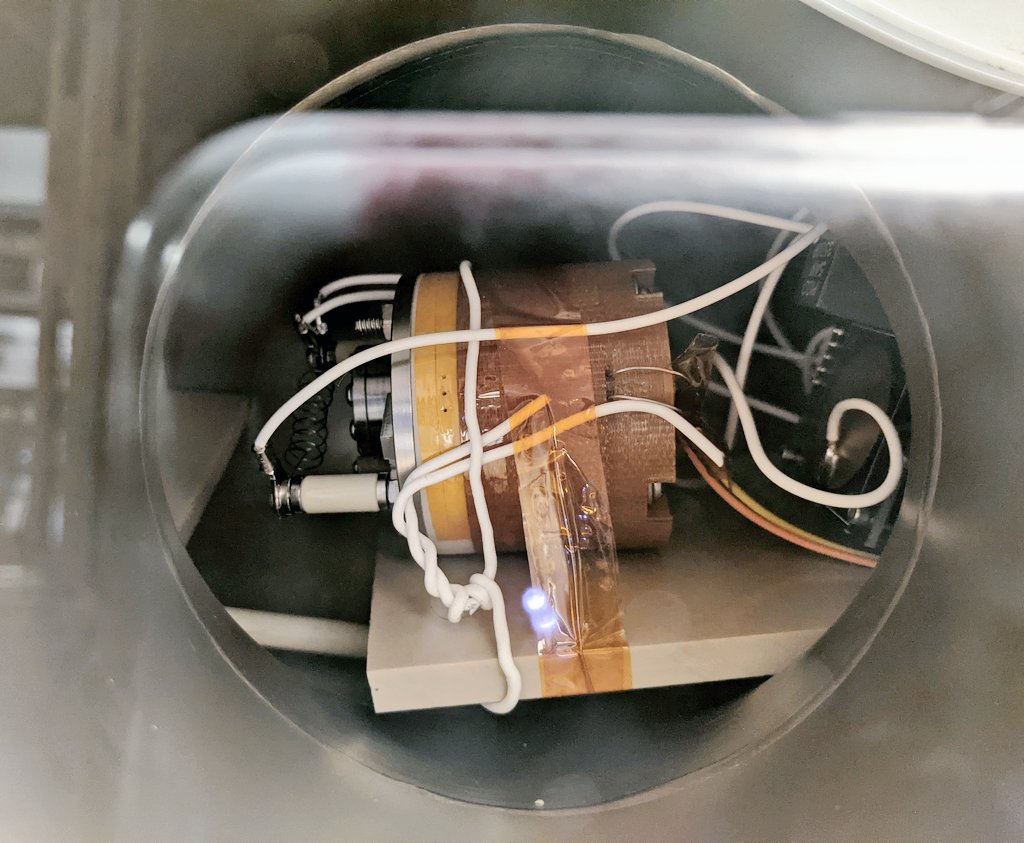
Pumpdown ended up being significantly smoother and faster than all prior four Adamantane sublimation and discharge tests with the test cell. This is most likely due to the fact that the internal gas pathways are much more complex in the thruster system than the simple discharge cell, significantly reducing the effective leak rate from the system. In preliminary testing with the discharge cell, I could only reach mid-10^-4 Torr at best during pumpdown with ambient as low as 11C. However, with the full thruster assembly, I could easily reach 1×10^-6 Torr, which is exactly where I wanted to be before turning the system on.
After full vacuum was reached, the filament supply was first powered on. I found that my benchtop supply was actually a bit laggy, resulting in much faster heating of the filament than I was aiming for. However, there were no further issues, and I adjusted the power back down to get a low-glow from the filament. Next, the +HV supply for the discharge was turned on. I first adjusted the supply to a 2kV, to verify there was no breakdown prior to turning on the sublimation heater.
Finally, the sublimation heater was turned on with 3.5W of power. After a minute or two, the vacuum pressure began to rise, eventually settling at the mid 10^-4 Torr range, indicating successful controlled sublimation and fuel delivery with the SFDS. Monitoring the HV discharge supply readout however, there was no indication of a discharge.
Waiting for several minutes, I brought the HV supply up to the max voltage of 5kV. Still nothing. Since the benchtop supply was maxed out for the heater, and the HV discharge supply was also maxed out, the last option was to increase filament power, with the hope that more electrons would allow for ionization of the gas.
I slowly brought up filament power. As filament power rose higher, I noticed that the discharge power started to drop, which was an indication that loading on the supply was occurring due to current flow from ionization. However, no discharge. Finally, I brought the filament power up to 50W, achieving a very bright glow. Discharge voltage began to rapidly drop, and eventually stabilized at 500-600V, indicating actual sustained ionization and discharge. Success!
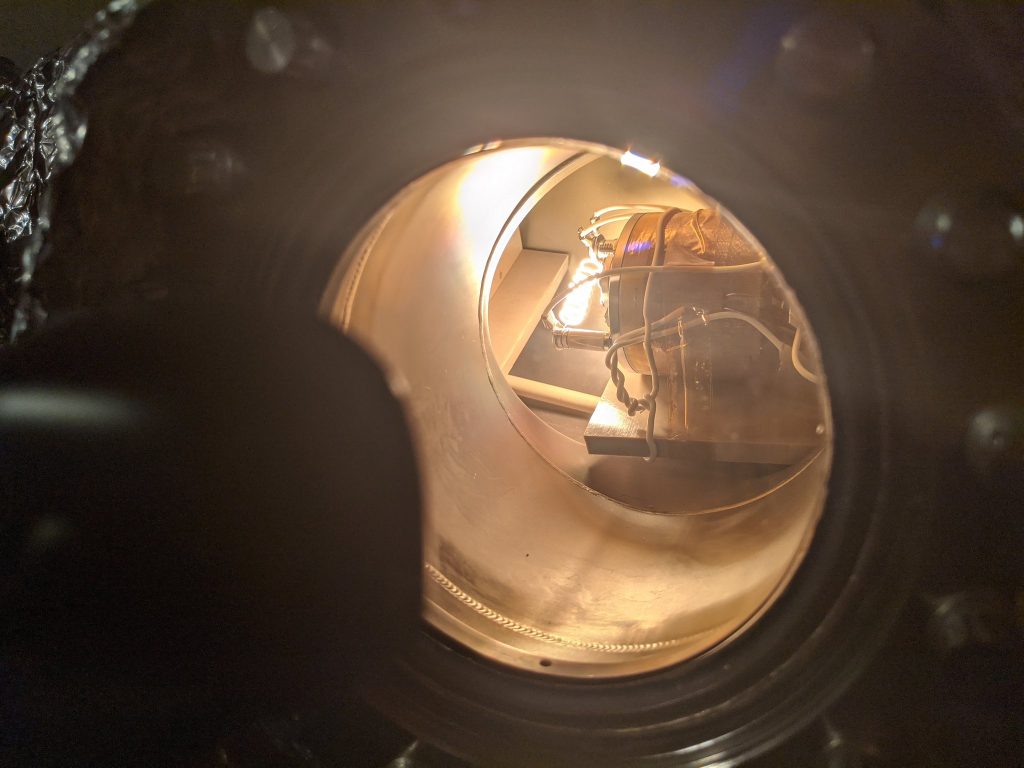
Unfortunately, due to the intense light output from the filament, and the extremely low power of the discharge, the actual discharge is not observable. For this test, I also decided to set up the Faraday cup just in case I would see any beam during the test, read through a +/-500uA galvanometer. This was a crucial decision, because looking over to the meter, I saw beam! +120uA of beam current!
Over the coarse of the test, I further verified beam by changing parameters and observing the current and discharge power. When filament power was reduced below some threshold, beam would cease and discharge voltage would rise. When I varied the discharge power at max filament voltage, beam currently would smoothly track, over a range of 100-140uA. Finally, at the end of the test, the Adamantane fuel ran out, indicated by a drop in beam current, increase in discharge voltage, and decrease in vacuum pressure.
During the test, stable ignition and beam was actually established and verified at only 2W of discharge power, using actively sublimated Adamantane fuel from the Sublimation Fuel Delivery System and run with a Tungsten filament neutralizer.
The success of this first test has massive implications for the ADAMANT Series, validating key design concepts. With so little data on Adamantane on the field, I went into this near blind with many unknowns, working with best educated guesses and intuition from prior experience. However, my intuition paid off this time, successfully operating the most complex thruster system I have ever designed to date.
I completed the full EHT1 design at the end of December. Only two months later, AIS has run numerous successful sublimation and discharge tests with Adamantane, leading up to ignition with this highly unconventional Hall thruster, and pioneering a path to the first Adamantane fueled ultra-low power micro Hall thrusters for small Cubesats, and officially leading development of the only Adamantane fueled EP systems on the market for satellites.
AIS is truly forging its own unique path, and actually breaking some truly new ground and developments in the field of electric propulsion.