A critical part of the preparation for the AIS-ILIS1 ionic liquid ion source electrospray thruster testing is fueling the thruster. There are numerous ways to do it, and after much though, I have decided upon one way that will balance reliability, cost, and hopefully functionality. Below is the first look at the ILIS1 vacuum fueling station design. A simple servo driven linear actuator pusher is mounted on a Teflon plate, with guide channels routed for the emitter and reservoir, and two drilled cups at the end for the fuel.
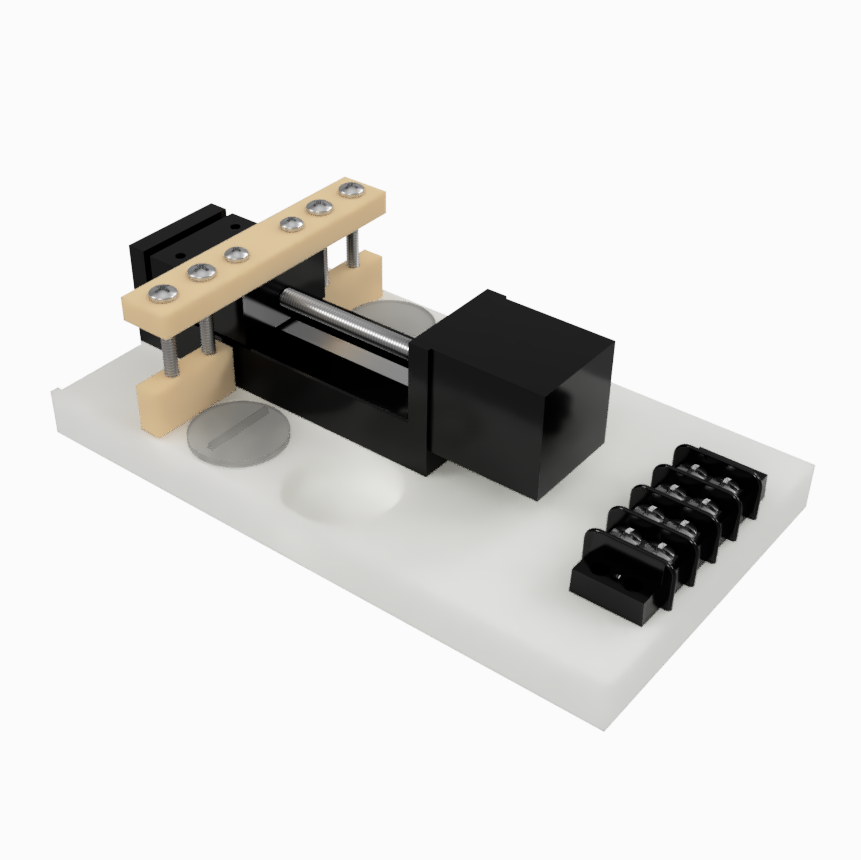
The fuel and glass thruster pieces will be degassed separately for several hours at high vacuum, then the emitter and reservoir will be slowly dropped into the fuel, allowing them to saturate while further degassing for additional time. Degassing is important for two reasons. One is to remove any adsorbed water vapor and gas in the fuel, which could cause issues during operation, including spurious droplet emissions which could lead to arcing and damage of the emitter. The second is to remove any air trapped in the pores of the porous glass structures, so that they saturate completely when dropped into the fuel.
The major parts are already ordered and on the way, and I am expecting to complete the build and run a couple of simple tests within the next few weeks to gear up for my first thruster fueling attempt prior to assembly for the first ignition test.