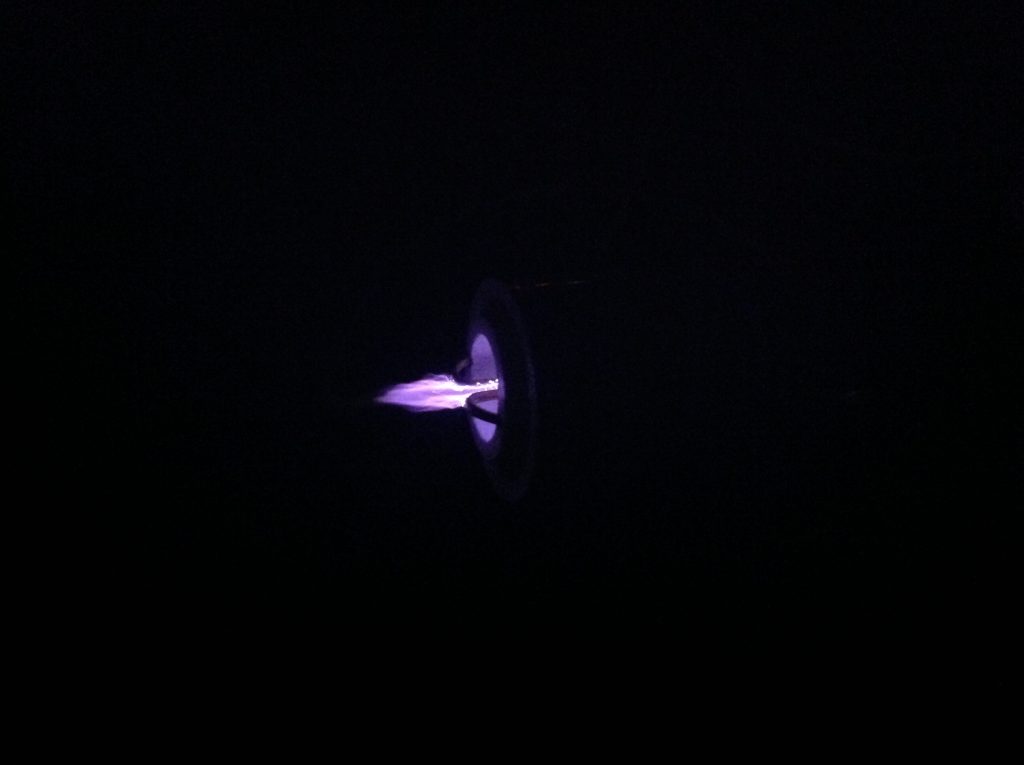
INTRODUCTION TO GLIDING ARC DISCHARGE
Gliding arc discharge (or GAD) plasma is a special type of atmospheric non-thermal plasma, that has many practical applications in research and industry over a wide and diverse range of subjects, including surface activation, surface modification, printing, sterilization, hydrocarbon reforming, enhanced combustion, waste treatment, and many others. This simple yet powerful tool can very easily and readily be explored at home on an extremely low budget, and can be used for a diverse range of DIY science studies and experiments. While custom industrial or lab systems can cost many thousands of dollars, low and high power systems can be built very easily at home for only a few dollars using common everyday materials, and are just as effective. This DIY Science page will cover the build and demonstration of a simple, low-powered handheld demo unit.
First off, what is exactly is gliding arc discharge? As mentioned above, gliding arc is a type of atmospheric non-thermal plasma. Atmospheric refers to the pressure range that it operates at, meaning standard atmosphere pressure. Essentially, no vacuum is needed for this plasma system. A unique feature about this plasma, as opposed to other typical “hot” arcs that are often seen, is that it is non-thermal, meaning that the plasma is non-equilibrium (not in thermodynamic equilibrium) as the electron temperatures in the plasma are much hotter than the bulk ion temperatures. Since only the electrons are thermalized and not the bulk ions from the injected gas, the average temperature of the plasma is close to room temperature. This allows for some very interesting applications in surface treatment and modification of materials that are particularly sensitive to temperature, where normal thermal treatments cannot be used.
How is the non-thermal plasma generated? Below shows a basic overview diagram of a gliding arc discharge plasma system:
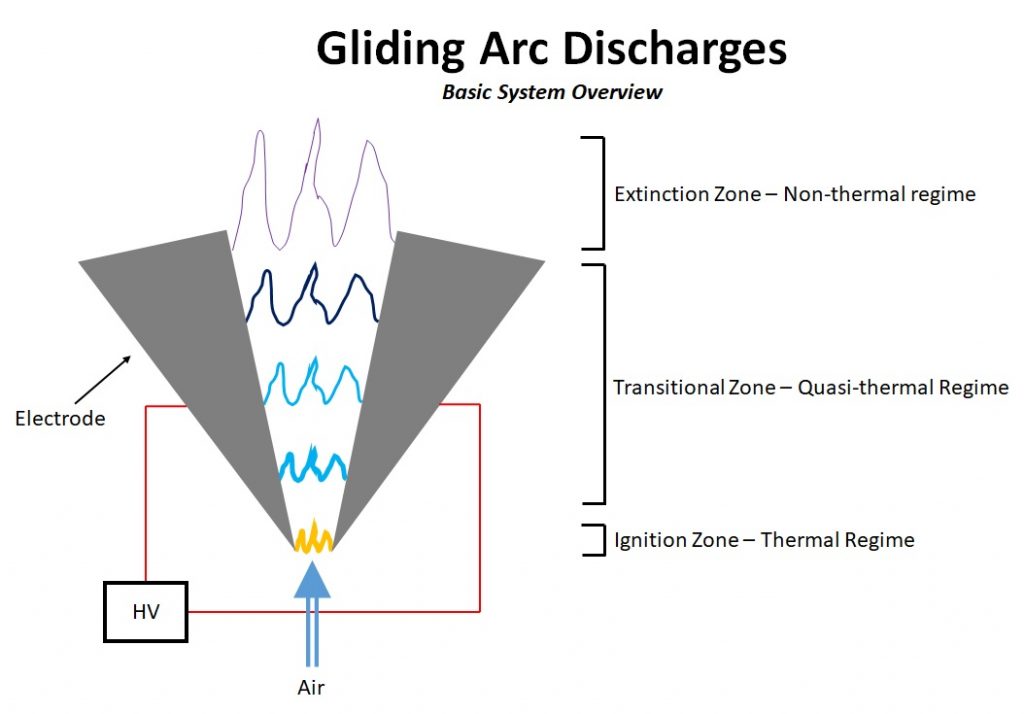
As can be seen from the diagram, a gliding arc system is conceptually very simple. It consists of two diverging metal electrodes, a high voltage supply, and a gas supply. Often times, plain air is used, although any gas can be used, depending on the effect desired. For a highly reactive plasma, wet air or even steam is used. For non-ozone generating plasmas, gases such as Helium or Argon can be used. Additional process gases can be injected, like fuels or hydrocarbons, for either hydrocarbon reforming, or plasma-enhanced combustion. In this overview, we will be exploring the most common and basic application, using a planar electrode system for surface treatment to enhance wettability.
There are several different regions where the initial arc undergoes changes. The ignition zone is the area where the arc is first struck at the closest point between the diverging electrodes. During this brief time, the arc acts as a thermal plasma. As the process gas (in this case plain air) pushes the arc up the electrodes, the arc expands, transitioning to a quasi-thermal plasma in the transitional zone between the diverging electrodes, and finally to a non-thermal plasma in the extinction zone, where the arc terminates. It is in this extinction zone where surface treatment takes place.
The arc formation and extinction process happens over a short period of time, where the arc forms, gets blown up the electrodes, extinguishes, reignites, and repeats. In essence, a gliding arc discharge is exactly an air-assisted Jacob’s ladder. With high enough airflow, the arc formation process happens faster and faster, up to several hundred Hz, and converts the arc from a thermal arc (like the big hot yellow arcs often seen with normal Jacob’s ladders), to the cool, purple (for air), non-thermal plasma arc. Another advantage of gliding arc systems is also that AC or DC can be used (except for advanced topologies using magnetic stabilization, in which DC must be used). This means that a simple gliding arc can be driven directly from the output of a high voltage transformer without the need for rectification.
Now that the basics are covered, let’s dive into this first simple demo unit build.
HANDHELD GLIDING ARC TREATER ASSEMBLY
The goal of this particular build was to make a very cheap and easy-to-construct low-power handheld demo unit for simple small-scale surface activation experiments. For ease of creating a simple handheld form factor, pvc pipe and adapters were used to build the plasma treater. Banana plugs are used for the high voltage input, and copper foil tape is run down the inside of the pvc body to provide connections for the removable electrode assembly at the end.
The front electrode assembly is made as a modular, removable part consisting of a pvc adapter coupling with holes drilled for electrode mounting, and brass electrodes made from bent 1/16″ brass rod. The ends at the ignition zone stick out of the pvc coupling to make contact with the copper foil contacts at the end of the main handheld unit. Additional insulation can be added after as needed:
The air supply for the unit is provided from a salvaged vacuum blower unit. The high voltage is supplied from a 6kV, 15mA high voltage transformer, unrectified, and current limited for safety. Everything was salvaged from electronics scrap, with basic hardware, for almost no cost. The pushbotton located on the handle of the plasma treater controls a relay in the power supply which turns on and off the high voltage for the arc manually. The power supply also has a switch that allows between manual arc mode, and auto arc mode (constantly on) SAFETY IS ABSOLUTELY CRITICAL! NEVER USE A SUPPLY THAT PROVIDES LETHAL AMOUNTS OF CURRENT OR AT HIGH POWER BEYOND MORE THAN A FEW TENS OF WATTS!
Finally, a few shots of the handheld treater system in action with the arc on:
With the demo unit built, let’s look at a simple experiment demonstrating a practical application of the technology for enhanced wettability via surface activation.
ENHANCED WETTABILITY VIA SURFACE ACTIVATION
This short demo video shows a simple experiment that can be done to look at the effects of enhanced wettability via surface activation. The plasma activates the substrate surface by raising its surface energy level above that of the liquid applied. Surface energy is typically measured in dynes/cm. This can include water, dyes, inks, adhesives, or any other coating. This technique is particularly useful for printing on plastics, which have very low surface energy, making it very difficult to wet or coat with inks or glues. Metals and glass typically have very high surface energies, in the hundreds to thousands of dynes/cm range. However, many plastics only have surface energies of several tens of dynes/cm. Teflon is one of the most difficult to coat due to its extremely low surface energy of only 19 dynes/cm, which is why it is such an effective non-stick surface. This can most readily be seen by applying the liquid to the surface, where beading will occur, as opposed to a uniform, thin coating spread over the surface.
A very common method of testing surface energy and activation of a surface in materials science is the contact angle test. This can be done with a simple syringe and water. The contact angle test measures the angle created between the surface of the substrate and the liquid applied. A high contact angle, where the drop is more circular, mean very low surface activation, or that the surface is hydrophobic. A very low contact angle, with the water drop flat on the surface, means that the surface energy has been raised at or above the level of the liquid applied. In the case of water, the surface has become hydrophilic.
In this test video, common printer paper is treated with the handheld unit to enhance surface wettability, measured with the contact angle test with blue-dyed water:
As can be seen in the video, the first water drop on the untreated surface beads up, and does not readily spread or absorb into the paper. However, after plasma treatment, the water drop flattens out and coats the surface of the treated paper immediately. Also can be observed is the fact that the paper is completely undamaged from the plasma treatment. Non-thermal atmospheric plasma treatment has the ability to only effect the very surface layers of a material without changing the bulk properties of the material itself, and does not leave any visible or noticeable damage to the surface as a result.
GOING FURTHER
Now that we have covered the basics of atmospheric non-thermal gliding arc discharge plasma, and provided a simple, low-powered hand-held demo unit build for practical experimentation at home, what can be done with the device? In the next DIY Science segments, we will be exploring the build of larger and much higher powered units for faster activation of larger surfaces. While this demo unit is useful for small examples with simple materials such as paper, plastics such as Teflon require a higher power unit for more effective activation. This can be used for printing on plastics, gluing plastics, coatings, as well as exploring some more advanced sciences such as paper microfluidics, by using the gliding arc to activate paper surfaces for micro-channel wettability. In addition, advanced topologies, such as magnetic stabilization, or vortex stabilization, can be explored for areas such as hydrocarbon reforming, and enhanced combustion. All of these systems can be built extremely cheap and explored at home, and allow for demonstrations and exploration of advanced applications of atmospheric plasmas for the DIY maker.